With the CII-Godrej Green Business Center (CII-GBC) achieving the distinction of being the first Platinum Certified Building in India in 2003, the green building movement has witnessed remarkable progress during the past nearly two decades. Currently, India has over 7100-plus green building projects with over 8 billion square feet (0.75 billion m2) of green footprints. In recent years, with the concept of net zero energy building assuming importance, an exercise was undertaken to retrofit the CII-GBC into a net zero energy building.
Advancing Net Zero Energy Buildings in India
S Karthikeyan and Shivraj Dhaka
The article presents a brief account of this retrofitting exercise. CII-GBC has to its credit more than 25 net-zero energy building projects and is currently working with over 70 key corporates in India to convert their buildings/corporate offices into net zero energy buildings.
‘Net Zero Energy’ movement started in India with the launch of Net Zero Energy Building Rating system in 2018. CII-Godrej Green Business Center (GBC) is the first Platinum certified Green Building in India. The building achieved Platinum Green building rating in 2003 and demonstrated advanced green features. In fact, the CII-GBC headquarter building paved the path for green building movement in the country. Today, India has over 7100+ registered green building projects with over 8.0 billion square feet of green footprint.
It has been realized that the green buildings have now become a movement in India. Hence, it was decided to convert the CII-GBC into a “Net Zero Energy Building”, to further accelerate transformation in Indian building sector. Advanced technologies, which are robust and affordable, are available in the country and these can help buildings to achieve net zero energy performance. Coinciding with the 15st foundation day of GBC on August 31st, 2019, Mr. Jamshyd Godrej, Chairman, CII-Sohrabji Godrej GBC handed over the Plaque to Mr. Ajay Mishra, Special Chief Sectary, Govt of Telangana for achieving Net Zero Energy Status (Design).
Overview of CII-GBC
The built-up area of CII-Green Business Center (GBC) is 1,858 m2, out of which 1,115 m2 is fully air-conditioned (centralized cooling system). The building is designed for day-time occupancy of 100 persons. Building envelope (wall, roof and glazing) is energy efficient and designed for maximum daylighting for all regularly-occupied spaces. Glass has been installed considering right orientation, more glass has been provided in north – harnessing daylight without heat.
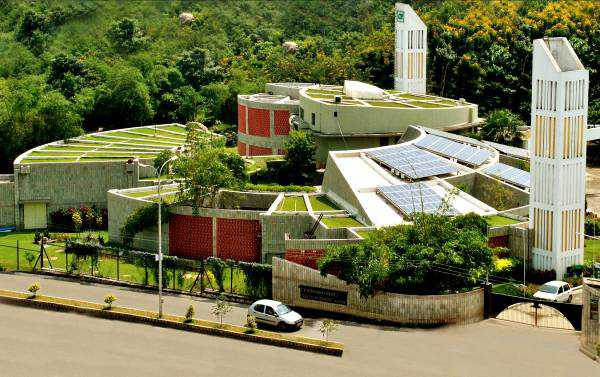
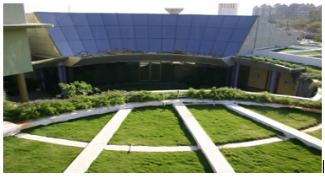
Fig 1 Headquarter of IGBC –India’s first green building (rooftop covered with vegetation to mitigate urban heat-island effect.
Strategies for Achieving Net Zero Energy Status
Energy efficiency is of paramount importance for achieving Net Zero Energy performance. CII-GBC was designed with energy efficient measures and has demonstrated more than 20% energy savings over the baseline defined in ECBC 2017 (latest Energy Conservation Building Code of India). Retrofitting strategy developed to further reduce energy demand and to increase use of renewable energy, following measures were suggested for implementation:
- Retrofitting of lighting (interior and exterior) system
- Replacement of air-conditioning system (chiller plant)
- Commissioning of advanced BMS system for optimised building performance
- Increasing capacity of on-site Renewable Energy generation.

Fig 2 Strategies adopted for reducing energy demand to convert the building into Net Zero Energy
Energy end-use summary and load profile were recorded, and deep analysis performed to understand hourly energy use. The peak load is 100 kW. Maximum demand occurs during the daytime, cooling system (chiller and air handling unit) are the main energy guzzlers.
Retrofitting of Lighting and Cooling system:
Completely automated CFL-based lighting fixtures (with dimming control, integrated with daylight and occupancy sensor) were installed in 2003. Globally, lighting system has witnessed complete transformation owing to introduction of LED-based lighting system which in fact reduces lighting load in buildings drastically.
Lighting system was retrofitted in 2018 and it has drastically reduced the load from 16.5 kW to 3.5 kW. LPD (Lighting Power Density) is less than 0.4 W/sq.ft. Thorough analysis (thermography) was performed before retrofitting the lighting system. Temperature of lighting fixture in case of CFL based lighting was recorded 510C, whereas the temperature of LED lighting fixture was 290C. This led reduction in cooling load by 4%.
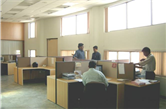
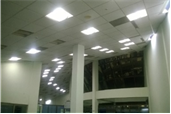
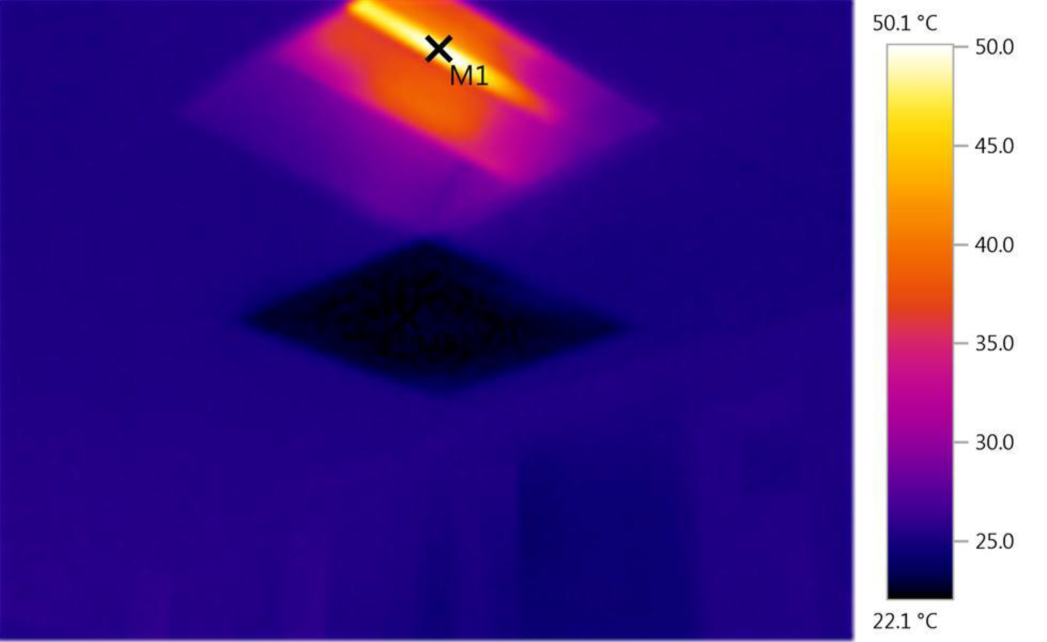
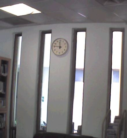
Fig 3 Daylighting through vision glazing, CLF-based lighting fixtures (& thermography) before retrofitting and LED-based fixtures after retrofitting (left to right)
The whole chiller plant was retrofitted including chillers, pumps and cooling tower with the most advanced and energy efficient system. The system is integrated with the wind towers (passive cooling system) that consciously supply pre-cooled fresh air. Two water-cooled screw chillers (2x49TR, COP of chiller is 4.85, iKW/TR is 0.725 at 100% loading) were installed. Since, most of the time, building operates at part load, chillers were selected giving more emphasis on part load performance (IPLV is 6.58 and ikW/TR at part load is 0.534). High efficiency pumps (IE4 motor) were installed for chillers and cooling towers, integrated with VFD to optimize the performance.
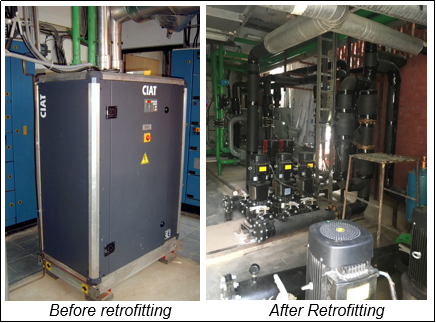
Fig 4 Chiller before and after retrofitting
Commissioning of advanced BMS system:
A sophisticated Building Management System (BMS) system was commissioned to optimize energy performance. It is estimated that an integrated BMS system can save 8-10% energy in commercial buildings. Chiller plant, AHUs and indoor and outdoor environmental variables are being continuously monitored, Then, the recorded data are used to analyse the performance
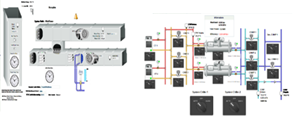
Fig 5 BMS system to meter and monitor energy and IEQ at each mode
Increased on-site Renewable Energy generation:
Since inception in 2003, CII-GBC has been promoting the use of renewable energy sources. Earlier, the SPV capacity was 24 kWp which helped in off-setting grid energy use by 21%. For a Net Zero Energy Building, it is mandatory to off-set 100% grid energy use by renewable energy (RE). Hence, it was decided to opt new technology that can enhance RE generation from the roof-top (1,175 m2 ). Initially, a site assessment was carried out and potential RE technologies were studied. Bifacial Solar PV technology was adopted which had promising efficiency (high electricity generation).
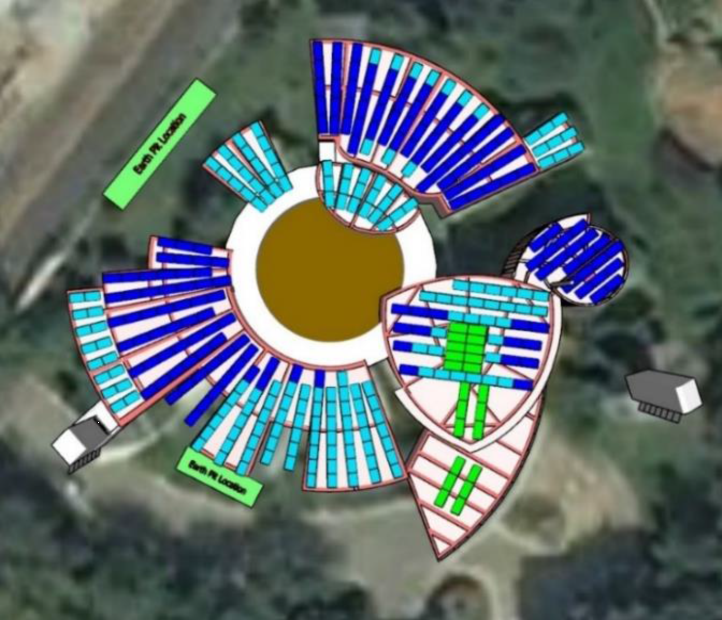
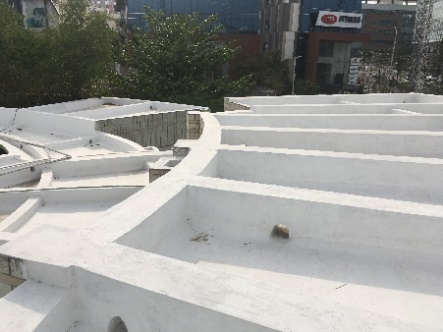
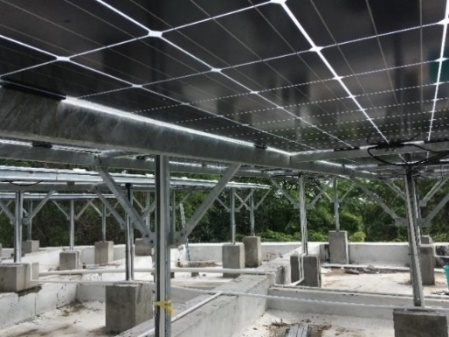
Fig 6 Atop covered with SPV system, high SRI coating and bi-facial SPV system
Bifacial solar PV is a transparent and frameless module and unlike regular solar modules that come with a singular face for absorption of light. Bifacial solar modules are equipped to allow passage of light from both the sides of solar cell and generate electricity from both sides (front and rear face of the module).
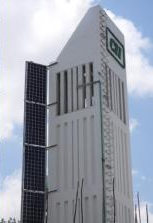

Fig 7 Horizontal and vertical installation of bifacial SPV system
This helps in increasing the efficiency per cell, resulting in an increase in the total energy generation along with reduced construction costs. In fact, to increase the yield on the backside, roof surfaces were coated with high SRI (more than 95) paint that reflects the radiation on back side of the module. The SPV system was installed at 1.5 m height from the roof, so that diffused radiation will fall on back side of the SPV modules. Total 130 kWp (efficiency of module is 22.3% which is higher than the conventional module-18.6% ) capacity of onsite bifacial SPV was installed (over roof-top and wind towers) and 8 kWp of old SPV system commissioned (on utility room). Thus, the total SPV system capacity is 138 kWp.
Till July 2020, the SPV system was off-grid connected, the unique feature ‘curtailment of power’ ensured energy generation only to meet the requirement. Grid connected net metering was installed in July 2019 and since then the building only uses RE to fulfil energy usage and excess energy is fed to the grid. On few occasions, when RE generation is insufficient to meet the demand, power is drawn from grid.
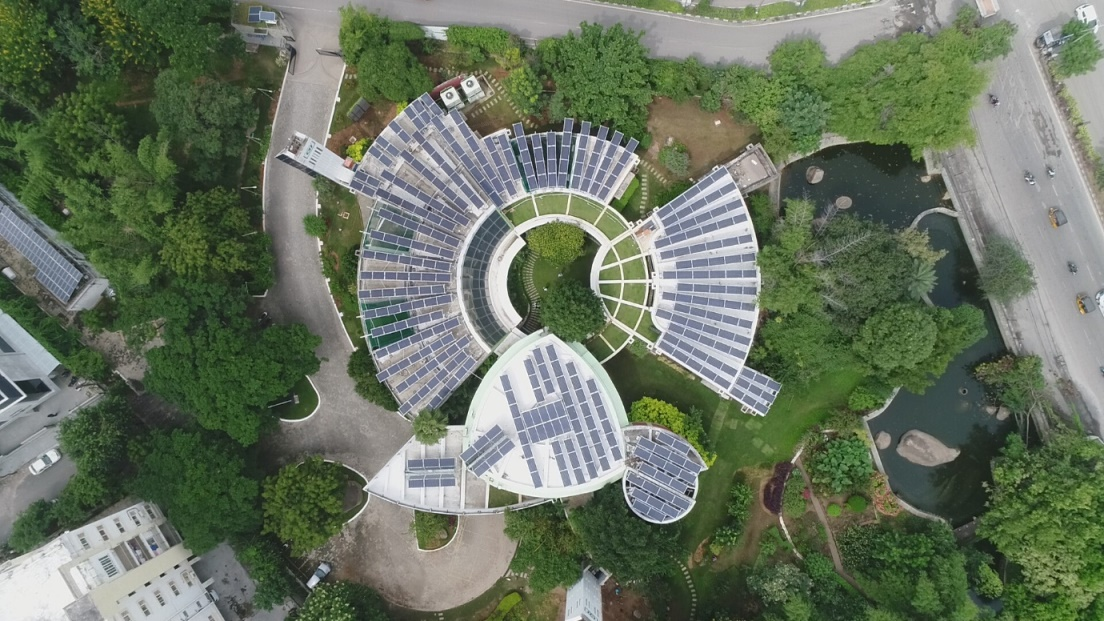
Fig 8 Arial view of the CII-GBC
Net Zero Energy Buildings in India
CII-GBC has to its credit more than 25 net zero energy building projects and is currently working with over 70 key corporates in India to convert their buildings/corporate offices into net zero energy buildings. From the snapshots of six net zero energy buildings provided in Fig 9, it is evident that these buildings can be of any type (residential, commercial – hotel, hospital, IT/ITE, offices etc. and industrial) and can operate well in any climatic region of India. These certified net zero energy buildings have demonstrated significant energy savings and offset 100% of their grid energy consumption through renewable sources. It is observed that industrial buildings, warehouses, and day-time offices can achieve net zero energy status and also gain more than 30-40% operational savings.
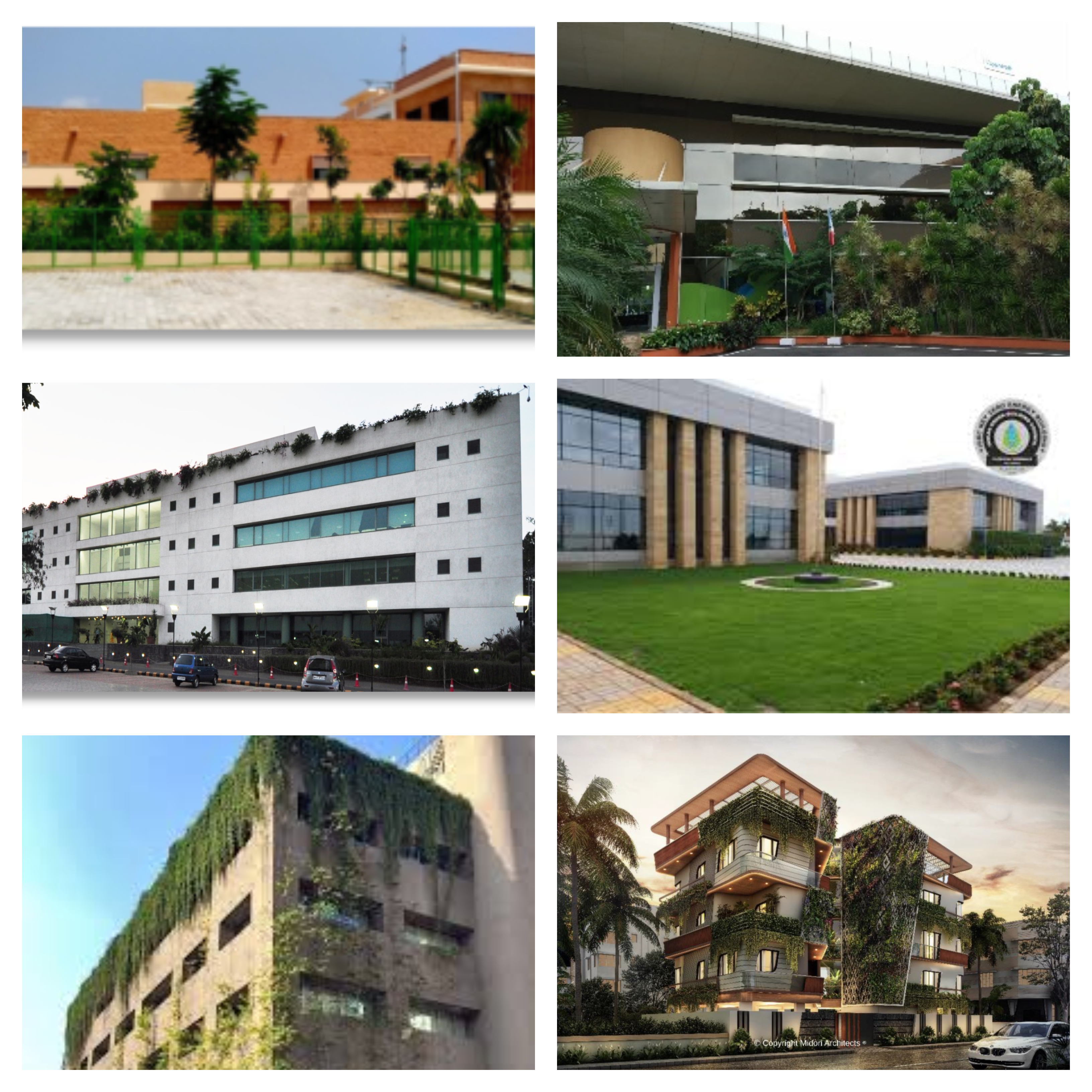
Fig 9 Net Zero Energy Buildings in India
Conclusion
Net Zero Energy Buildings offer immense tangible benefits, especially in reducing operational expenditure. Considering the successful experience of CII-GBC, residential, commercial and industrial projects should come forward to have their projects future-ready for technology and performance. In case of new building projects, it is important to embed passive design features which optimize building design and then consider energy efficiency measures for implementation. In existing building projects, retrofitting would lead to significant energy savings. Hence, primarily; energy efficiency should be focused to reduce energy demand and later RE sources shall be deployed to off-set grid energy use by renewable (on-site or off-site RE). Net Zero Energy Buildings are the future!
Authors
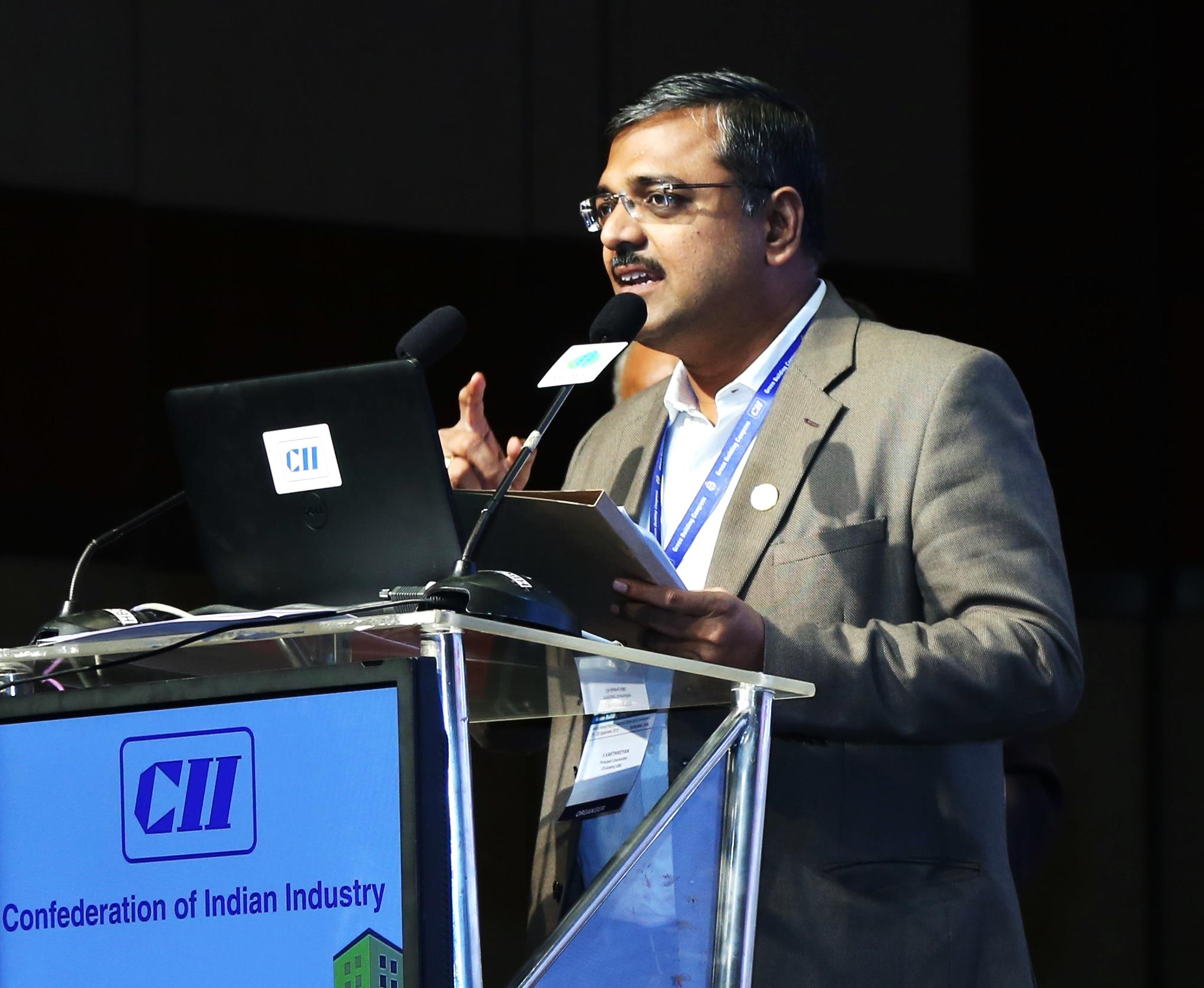
Mr. Karthikeyan is a Principal Counsellor in CII-Sohrabji Godrej Green Business Centre (CII-Godrej GBC), India. He is a mechanical Engineer with master’s degree in energy conservation and management. He has over 20 years of experience in industrial energy efficiency, green buildings and ecolabelling. Presently, he is leading the facilitation and certification of green building services in CII. He has been instrumental in designing and developing the GreenPro – Indian Ecolabel, which aims at facilitating green product market transformation in India.
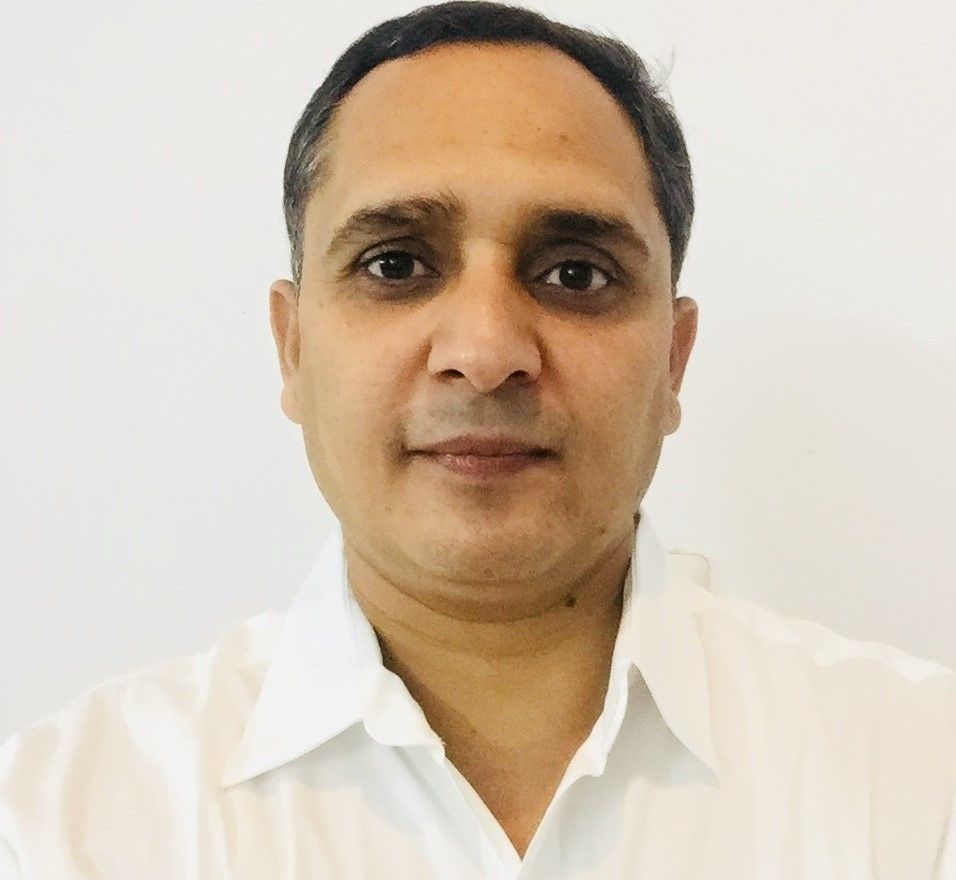
Dr Shivraj Dhaka has over 14 years of experience in industry and academia. He has been involved in research, especially on building, energy and environment since 2008 and has published over 20 research articles. Dr Shivraj was awarded DAAD Fellowship, Germany in 2012 for research on thermal comfort at Karlsruhe Institute of Technology (KIT), Germany. At Indian Green Building Council (IGBC), Shivraj leads green building certification services, especially for data centers, green factories, net zero energy and water and existing buildings (O&M). He has facilitated more than 300+ green buildings projects across the country
J. M.
October 5 2023Mumbai
Dear Sir,
ReplyHearty congratulations for the Volume 1, No.2 of LCCF Newsletter. I have read with interest the thought-provoking Edit and the development of Nano concrete aggregates.
However, I have need one clarification on the special feature ‘Advancing Net Zero Energy Buildings in India’ contributed by S Karthikeyan and Shivraj Dhaka. The article describes retrofitting measures of CIII-GBC headquarter building into a net-zero operational energy building and further states that more than 25 such net-zero operational energy building projects are being presently undertaken. Unfortunately, article is silent about the cost economics of the retrofitting exercise. Also, it does not mention the period required for recovering the investment made for retrofitting.
I request the authors to kindly throw light on the above aspects.
S Karthikeyan
October 7 2023Principal Counsellor, CII-Godrej Green Business Center, Hyderabad
Dear Sir,
ReplyThanks for sharing the feedback. Specifically we did not want to talk about the cost economics in this article, because we believed that the attention would completely get diverted to costing instead of the technical feasibility of the whole concept.
Typically, the energy efficiency measures for reducing the energy consumption is very attractive. The building projects implement the energy efficiency measures only if the payback period is less than 2 to 3 years. All the projects implemented in our building also had the similar payback period of less than 3 years. We invested about Rs 75 lakhs for improving energy efficiency including replacement of the old inefficient chiller of capacity about 50 TR and other measures related to lighting systems, pumps etc.
The investment for renewable energy generation will have longer payback period depending upon the generation potential and the tariff regime in their state etc. In our case the payback period is about 7 years and we invested about Rs 125 Lakhs for installing renewable energy generation capacity of about 135 KWp. Still it is attractive considering the life cycle cost.
Hope this meets his requirement.