The climate change phenomenon has been providing consistent warning signals to us, highlighting the fact that the environmental health of the planet is becoming more and more fragile day-by-day. The earlier records of greenhouse gas emissions, temperature extremes, sea level rise, ocean acidification, etc. are getting broken. Take for example, the latest report from the World Meteorological Organization (WMO), which testified that 2023 was the warmest year in the 174-year observational records, with the global average near-surface temperature reaching at 1.45°C above the pre-industrial (1850–1900) average [1]. In India too, such records are being broken. The India Meteorological Department (IMD) reported that while the north-west and the central India witnessed the highest temperatures in the past 122 years during April 2022, the year 2023 saw the warmest February since 1901[2]!
Simultaneously, news reports are emerging on the scarcity of water being experienced in different parts of the world. In the latest issue of Sustainable Switch published by Reuter Digital, Ms Sharon Kimathi, Energy and ESG Editor, provides a glimpse of the water scarcity-like situation in four countries, which is reproduced below in brief:
- With the drought stretching into the fourth year, many areas in Alberta, Canada, particularly into the southern part of the province are facing water scarcity. Currently, Alberta is reportedly in the stage 4 (out of 5) in its water shortage management response plan.
- In Mexico, South America, water is receding from the vital desert oasis Cuatro Cienegas, affecting the alfalfa crops, used to feed the livestock.
- In Chile, after 15 years of devastating drought, water reservoirs are running dry. The Cogoti reservoir in the Coquimbo region having a capacity of 150 million m3 is reported to be completely depleted.
- In Bengaluru, India, the main reservoir supplying drinking water is at 16% of its total capacity during the third week of March 2024.
Acute Water Scarcity in Bengaluru
As regards Bengaluru, the Indian media is abuzz with a plethora of reports, highlighting the possible root causes responsible for the current calamity and the difficulties being faced by the residents of the city. One of the main root causes for the state of affairs seems to be the lack of appropriate management of the city’s water resources and their distribution. It is reported that nearly 50% of the city’s water supply is extracted from the ground through tube wells. Bengaluru is dotted with a large number of cascading lakes which through the underground channels had been the main source of the groundwater. Unfortunately, with uncontrolled urbanization and unauthorised encroachments in the catchment areas of the lakes, both treated and untreated water along with soil, clay, etc. found their way into the lakes increasing silt and debris accumulation. This resulted in reducing the effective water availability in the lakes. Further, it is reported that the leakages and unauthorised connections in the distribution network are responsible for as much as 30% ‘loss” of water!
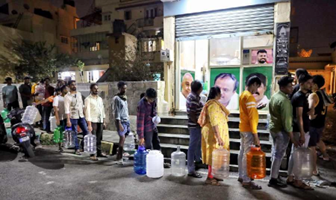
Bengaluru is facing one of the worst water crises in recent years
Besides Bengaluru, many major cities in the country are facing similar problems. The data from India Meteorological Department (IMD) showed that at least 540 districts across India have already started experiencing water stress in varying degrees even during the month of February [3]. Of these, 98 districts were facing extreme-to-severe-to-moderately dry conditions as on February 28, 2024. The water scarcity is likely to get aggravated during the remaining summer season from April to June 2024.
It is therefore highly essential that all-round efforts should be made to adopt the time-tested measures on universal basis such as vigorous drive to clean silt, clay and other debris from major water sources supplying drinking water; establish rainwater-water harvesting wherever possible, direct the industrial and commercial establishments to adopt rigorous water conservation measures, etc.
How to reduce water requirements during concrete construction?
Amongst different industries, the concrete industry is in a position to save considerable quantity of water by adopting simple conservation measures. During concrete construction, use of water become essential for three main activities:
- firstly, for the hydration of cementitious materials and providing desired workability for placing, compaction and finishing operations
- Secondly, for washing and cleaning of the mixer and other equipment, and
- thirdly, for the curing of concrete.
There is sufficient scope to reduce water usage in each of the above-mentioned activities. We sug-gest the following measures which will go a long way in reducing the water requirement during concrete construction:
1. Optimizing the use of mixing water
There is a deep-rooted tendency amongst different sections of the construction industry to use concrete having higher cement contents. This has been the bane of the erstwhile practice of using site-mixed concrete. Unfortunately, the same tendency continues even after the widespread use of ready-mixed concrete (RMC). It would not be an exaggeration to state that a majority of concrete mixes produced in the country through the RMC route contain higher cementitious contents, which demand higher water requirements. Furthermore, an undesirable practice of specifying concrete of one grade higher than structurally essential is in vogue in certain quarters to avoid possible failures! All such practices are leading to the use of concrete containing more than necessary quantities of cementitious materials and water. Most of such concretes tend to become prone to shrinkage cracking.
The best practice would be to undertake mix optimization exercise which involves achieving best possible particle packing of the aggregate skeleton so that there are least voids requiring the least amount of both cementitious materials and water. Further, one can make intelligent use of chemical admixture(s) to achieve the desired workability at the pouring site.
2. Reusing wash water obtained from Reclaimer and filter press
The RMC industry has spread its tentacles in major urban centres in India. Transit mixers plying on the urban roads is a common sight today. These trucks carry fresh concrete from RMC plants and after pouring the same at the construction site, the mixer drivers pour around 300-500 litres of water in the transit mixers from the drum mounted on the top of the mixer. The objective is to avoid build-up of cementitious paste inside of the mixer. Once the truck comes back to the RMC plant, the transit mixer drum empties its contents in the settlement pits. These pits usually have two or more compartments, permitting the transfer of relatively clear water from one pit to the other. This relatively clear water is generally used for dust control and other cleaning activities. However, this is not an environmental friendly practice.
Here, there is a considerable scope for saving water. Firstly, the drums fitted on transit mix-ers need to carry lesser quantity of water, which is just sufficient to make a fluid paste of the remaining contents in the transit mixer. Secondly, a combination of a reclaimer system and filter press can be used to recycle the wash water and recover the cementitious paste and water separately. While the reclaimer separates out cementitious materials from the wash water, the filter press squeezes out the remaining water forcefully from the cementitious paste, thus removing almost the entire finer fractions from the wash water. As a result, both the finer fractions from the cementitious paste and cleaner water can be completely recycled and reused.
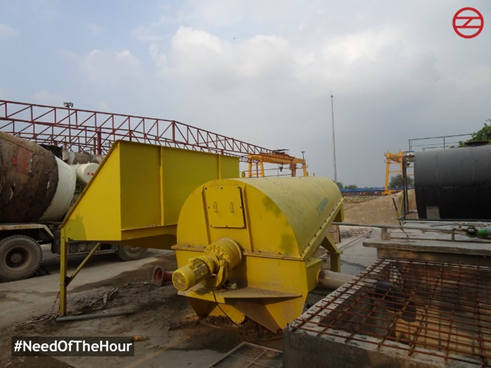
Fig 2: Reclaimer system used at a project site of Delhi Metro Rail Corporation
( Source :- https://twitter.com/OfficialDMRC/status/1320696993170112512https://twitter.com/OfficialDMRC/status/1320696993170112512
Certain progressive-minded RMC producers have already installed the reclaimer and filter press system in India on pilot-scale basis and these are reportedly functioning well. A detailed account of such a system was included in LCCF Newsletter issue Vol.1, No.3.
With the use of the combination of a reclaimer and filter press, it would be possible to save around 100-150 litres/m3 of concrete. Thus, for a RMC plant producing around 5,000 m3 of concrete per month, it would be possible to save at least 500,000 litres of water every month!
Incidentally, certain hydration stabilizing chemical admixtures (HSCA) are developed that can be used to effectively extend the working time of fresh concrete, especially when concrete is to be used for long-haul or hot-weather applications.
3. Use of chemical additives for internal curing and sealing of concrete
Curing is a process of deliberate control of moisture and temperature in freshly placed concrete to allow cement hydration and pozzolanic/hydraulic reactions (in case supplementary cementitious materials such as fly ash and ground slag are used) to occur so that concrete is able to develop the specified properties.
A guesstimate made by the present author indicated that the water required for curing concrete having 1m2 of surface area lie between 12-20 litres/m2 [4]. With around 1.5 billion m2 of construction space required to be built per year to cater to the growing urbanization needs in india, the guesstimate postulated that the yearly total water requirement for curing of concrete would be around 18-30 billion litres/annum up to 2040!
With the latest technical advances in the field of construction chemicals, it is now possible to drastically cut down on the water requirements for curing. Three options are available. First, ‘evaporation reducers’ can be spray-applied on the fresh concrete surface immediately after bleed water sheen has disappeared after finishing of concrete. ACI 308-R reported that evaporation reducers can reduce evaporation rates by as much as 65% [5]. Based on the market information, the cost of evaporation reducers in India is not high as it falls in the range of Rs 10 to 15/m2 of the surface area. Hence the use of this chemical would be quite effective during the initial stage after the initial setting to provide protection to the young concrete, which will go a long way in minimizing the occurrence of plastic shrinkage cracking. After the application of evaporation reducer, one can just cover the concrete surface with thin plastic sheets to protect the concrete from the adverse effects of the environment. Secondly, once the concrete is hardened, use of a curing compound – either wax-based on resin-based - could be quite effective.
Incidentally, internal curing of concrete can be achieved by using either water-saturated ag-gregates such as sintered fly ash aggregates or bloated clay aggregates or use of super-absorbent polymer as concrete admixture during mixing. In both these methods, water from saturated aggregates or from polymers is slowly released within the body of concrete as the hydration process progresses.
Thirdly, internal ‘sealing’ techniques are now available and can also be adopted. This involves adding water-soluble chemicals during mixing of concrete. Such addition reduces water evaporation as concrete is exposed to air drying.
Thus, the option of using different construction chemicals provides a good tool to save wa-ter required for curing of concrete.
It is our earnest request to all stakeholders in the concrete industry to start practicing the above measures rigorously to save precious water.
References
- Climate Change indicators reached record levels in 2023, Press Release, WMO,https://wmo.int/news/media-centre/climate-change-indicators
- Climate Summery for the month of February 2023, India Meteorological department,https://mausam.imd.gov.in/Forecast/marquee_data/IMD%20FEB23_Monthly_Clim_Summary.pdf
- 540 districts across India already under water stress: IMD data, The Times of India, March 3, 2024,http://timesofindia.indiatimes.com/articleshow/108173674.cms?utm_source=contentofinterest&utm_medium=text&utm_campaign=cppst
- Kulkarni, Vijay, Rough estimation of water requirements for concrete production and measures for conservation, LCCF Newsletter, Vol. 1, No.3, July-September 2022.
- ACI 308R-01, Guide to Curing Concrete, American Concrete Institute, USA