Following the well-known sustainability-centric principle ‘Recover, Recycle and Rebuild’, Godrej Construction has set up an automated Recycled Concrete Materials (RCM) manufacturing plant in Mumbai and has recycled over 25,000 metric tonnes of concrete debris till date. Using the recycled aggregates from this plant, the Company has produced a variety of prefabricated concrete products such as building blocks, pavers, culverts, Overhead Track Exhaust (OTE) ducts, etc., some which have received the BIS certification.
Precast Concrete Products from Recycled Aggregates : Noteworthy Example in Sustainability
Abhijeet Gawde and Anup Mathew
The article highlights that the quality of the precast products produced by using recycled aggregates is at par with those produced from conventional aggregates. It also describes the salient features of the joint Indo-Norwegian demonstration project, which proved that the concrete containing recycled aggregate has a higher CO2 binding capacity. Finally, for ensuring higher utilization of recycled aggregates in construction, the author suggests that the government and semi-government bodies need to implement certain policy issues.
Introduction
Globally, human beings consume billions of tonnes of natural resources annually, which cannot be replenished completely. As a result, the human race will eventually run out of these limited resources. It is therefore essential to consider ‘waste’ as an opportunity to ‘Recover, Reuse and Recycle’ rather than a waste that can be discarded. To maintain the right balance between the adverse effects of rapid urbanization, growth in population, increased natural resource consumption and the challenge of climate change, it is imperative to adopt a circular economy in our journey of achieving economic growth.
Globally, the construction sector is amongst the largest consumers of natural raw materials. It is a sector, which is vulnerable to raw material supply problems and price volatility. It therefore does make a sense to focus on resource efficiency, and the reuse of materials. With new buildings and infrastructure projects construction work on rise, the demand for building materials is expected to increase. This may result in acute shortage of building materials. Globally, it is now established that adopting improved construction process could reduce the adverse impacts on the environment and reusing construction and demolition (C&D) waste is a viable alternative.
As per the World Green Building Council’s report, building and construction sectors are responsible for 39% of all carbon emissions in the world, with operational emissions (from energy used to heat, cool and light buildings) accounting for 28%. The remaining 11% comes from embodied carbon emissions that are associated with materials and construction processes throughout the whole lifecycle of buildings. Broad-based recycling of construction materials coupled with smart design could substantially reduce CO2 emissions generated by buildings.
C&D Waste – A Resourceful Opportunity
According to a report released by the Centre for Science and Environment (CSE) in 2020, India recycles just one percent of its Construction and Demolition (C&D) waste1. As per the estimate prepared by Building Materials and Technology Promotion Council (BMTPC) and the Centre For Fly Ash Research and Management (C-FARM) in the year 2016, the C&D waste generated in India was approximately 165-175 million tonnes annually2. While Delhi NCR generates about 5,000 tonnes daily, Mumbai gets about 3,000 tonnes/day, followed by Kolkata at 2,000 tonnes/day and Chennai at 1,500 tonnes/day. However, the official recycling capacity is a mere 6,500 tonnes/day.
Management of C&D waste has become essential to ensure sustainable infrastructural growth across the globe. The major proportion of C&D waste comprises of debris generated from the demolition activities of old buildings, roads, bridges, etc. Inadequate management of the C&D waste can lead to disruption of natural resource cycles.
C&D waste can be considered as a resourceful opportunity with a potential of nearly 70% of waste that could be recovered using appropriate methods and guidelines during any demolition activity. Assessment of the structure by reputed structural consultant before demolition work is essential to recover most of the materials for recycling using suitable demolition method and segregating the waste generated at the source. These are key factors for the high level of C&D waste recovery.
In terms of waste streams, concrete, bricks, blocks and other fine materials form a major fraction in the overall C&D waste generated. The composition of C&D waste is highly variable depending upon the type of project, construction technique and site location of the project.
Godrej Construction Initiative – ‘Recover, Recycle and Rebuild’
Godrej has a distinction of being one of the leading corporate houses in India having strong commitment towards sustainable development and protecting the environment against the harmful effects of climate change. In line with its core values, Godrej Construction (GC) has implemented various initiatives across its different lines of businesses. One such recent initiative include establishment of an automated Recycled Concrete Materials (RCM) manufacturing plant in Mumbai.
Following the principles of “Recover, Recycle and Rebuild” and also that of circular economy, Godrej Construction commenced the practice of recycling concrete debris to produce various prefabricated concrete products such as building blocks, pavers, culverts, OTE ducts, and other customized precast concrete products having superior quality. These products are comparable both in strength and durability with other commercially available concrete products made using virgin aggregates.
The recycled concrete from concrete demolition waste is being used for making customized prefabricated concrete products such as box culverts and ducts. There are being used in some of the major infrastructure projects in Mumbai. Godrej Construction has recycled over 25,000 metric tonnes of concrete debris till date by implementing circular economy principles in their construction materials line of business. The Company has received certification from Bureau of Indian Standards (BIS) for a few variants of Company’s recycled concrete blocks. Godrej Construction is also collaborating with reputed agencies from Norway to render help in testing and developing these products as per international standards and global best practices.
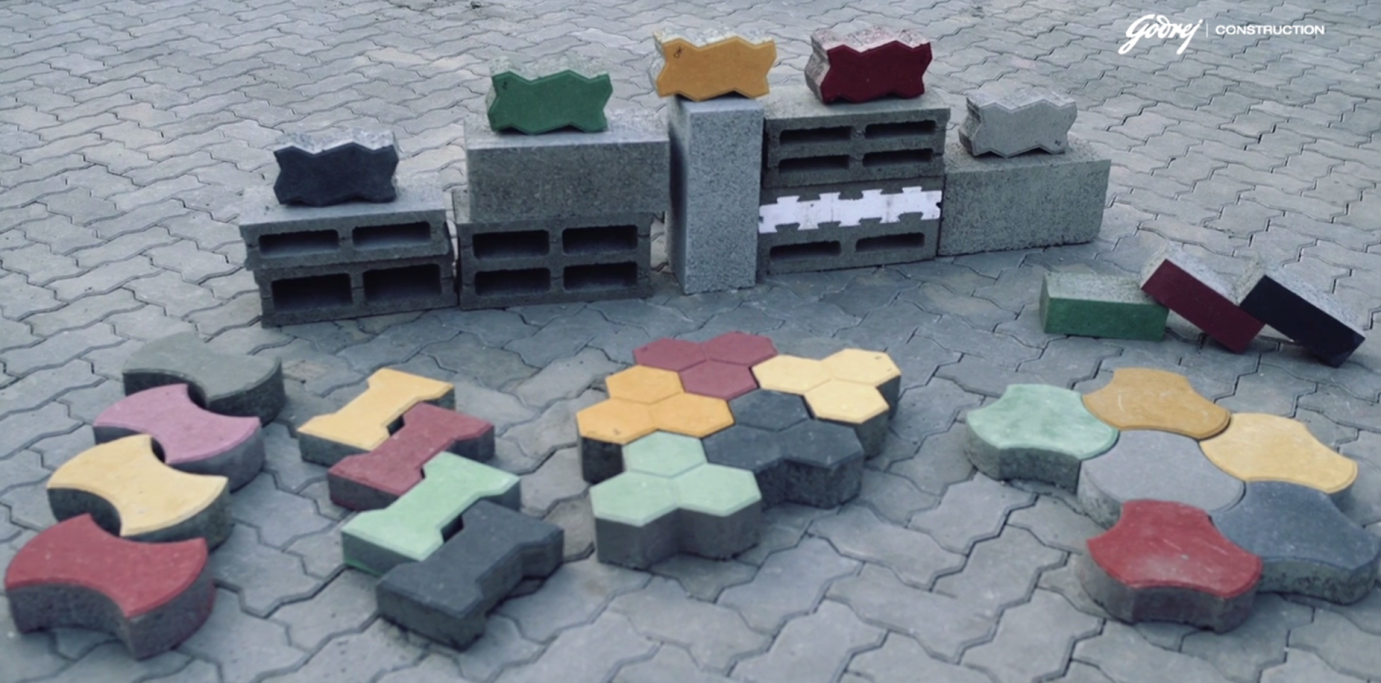
Photo 1: Different precast products produced by using RCA
Incidentally, Godrej Construction is one of the first in the RMC industry to switch to 100% green energy. The company’s Ready-Mix Concrete (RMC) plant, the Recycled Concrete Materials (RCM) plant and the common areas of Godrej Business District building in Mumbai are now powered by 100% renewable energy!
Godrej Construction has received the ‘GreenPro’ certificate from Indian Green Building Council (IGBC) for a variety of their RMC products such as Enviro TUFF, Xtra TUFF, Easy TUFF and other construction materials such as TUFF Blocks AAC, Recycled Concrete Blocks and Pavers making them beneficial for use in Green Buildings. Company’s three RMC plants in the Mumbai-MMR and Pune region have been commended with the ‘GreenPro’ Certification by Indian Green Building Council (IGBC).
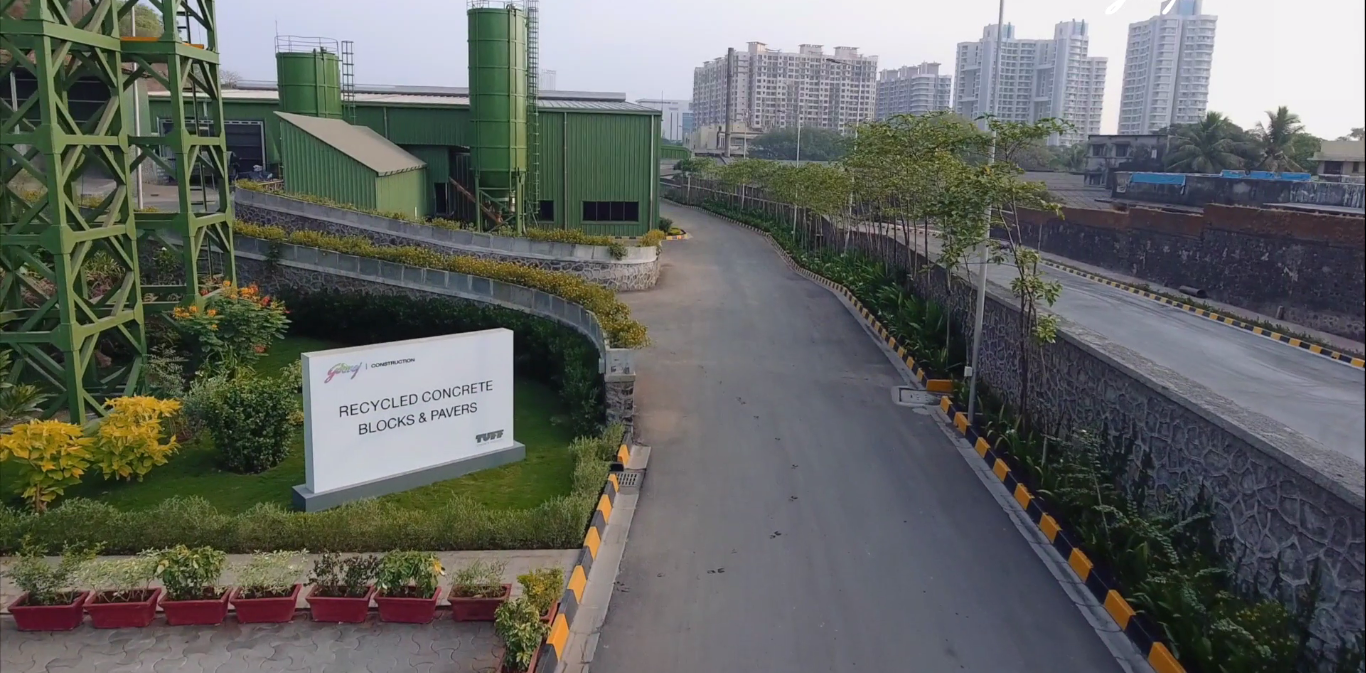
Photo 2: Demonstration Project on Use of RCA
A successful demonstration project was conducted on the RCA using fine aggregates produced at Godrej Construction’s Recycled Concrete Materials plant at Vikhroli Mumbai. For this project, Godrej Construction sought association with two leading organizations – the Central Public Works Department, Government of India and SINTEF, Norway. The latter is a world-renowned organization in scientific research on C&D waste and its practical applications.
A full-scale demonstration project on RCA was initiated under the joint Indo-Norwegian initiative. The main objectives of the project were to:
- demonstrate the value-added benefits of using RCA in making of recycled concrete products, and
- assess natural CO2 binding potential of RCA.
The demonstration project was carried out in two phases. In the first phase, two types of concrete blocks – one containing natural aggregates and other containing RCA – were produced at the Godrej plant. These were separately sampled for CO2 binding measurements and shipped to SINTEF Laboratory i Norway. The blocks were crushed and were exposed to CO2 exposure into patented test apparatus in SINTEF’s laboratory. The exposure involved changing relative humidity (RH), pressure, exposure period, etc. The results of CO2 uptake were observed at defined frequency are depicted in Figs 1 and 2.
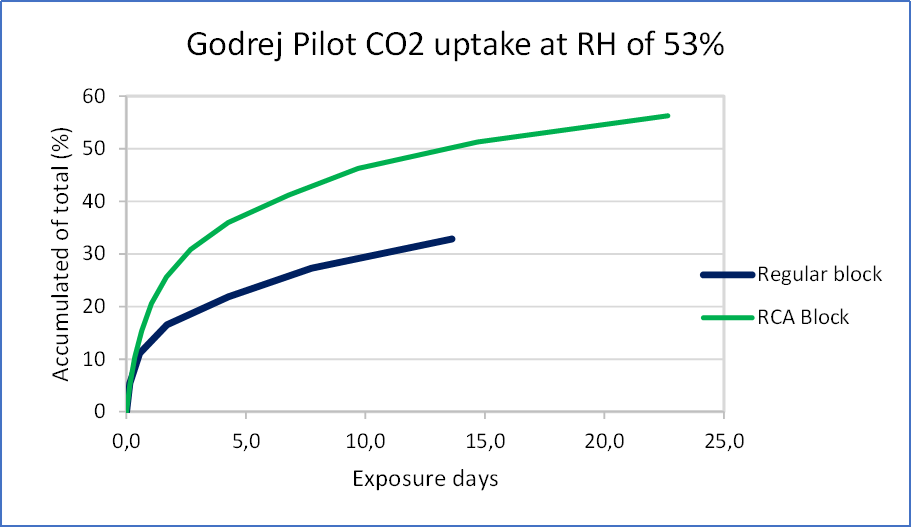
Fig 1 CO2 Uptake measurement results – relative humidity (RH) of 53%
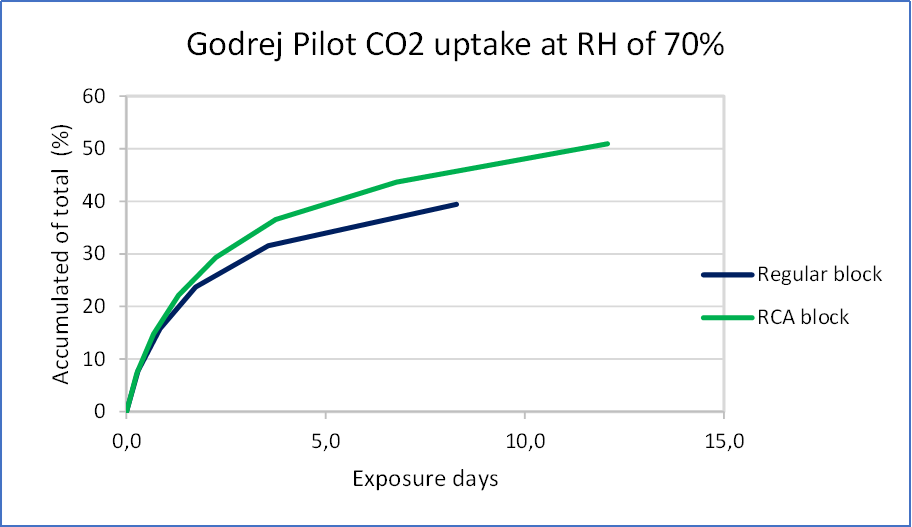
Fig 2 CO2 Uptake measurement results – relative humidity (RH) of 70%
The test results in Figs 1 and 2 reinforce the theory that concrete containing recycled aggregate has higher CO2 binding capacity owing to carbonation.
In the second phase of the demonstration project, concrete debris was collected from a demolition site of a hotel building in Mumbai. The structure was around 8 to 10 years old and was approximately 6.5 km away from the recycling plant. Ultrasonic pulse velocity and carbonation tests were carried out on the site before collecting the debris for ascertaining the quality of in-situ concrete.
The debris was then pulverized in the Godrej’s recycling plant and RCAs were produced. RCA sampling was done at defined interval during the production. Five samples were collected in an hour from different batches of production. The hourly samples were collected in different bags and labelled properly for ease of identification. Hourly samples were mixed with each other to make a composite sample for testing.
The composite samples were tested at 3rdparty laboratory for checking various physical properties of RCAs produced. The tests included sieve analysis conforming to IS 2386, Part 1, and other physical tests conforming to IS 2386, Part 3. The results of test are included in Table 1. The test results were encouraging and demonstrated that the RCAs produced through good quality feedstock and well controlled production process possessed properties more or less similar to those of naturally sourced aggregates.
Table 1:- Third-party test reports on physical properties of RCA
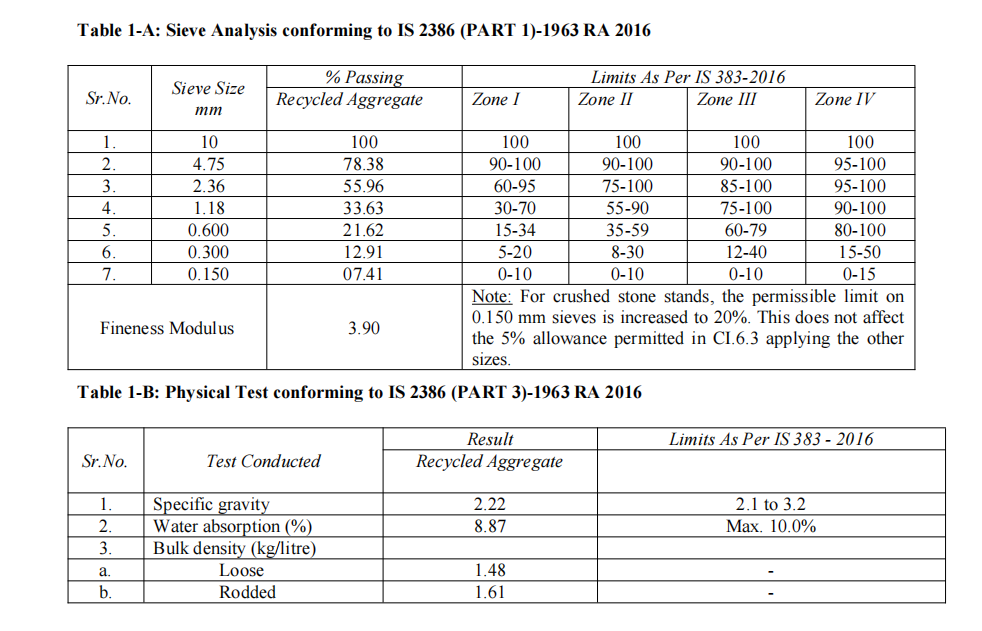
The fine aggregates obtained from RCAs were used in making solid concrete blocks. These recycled solid concrete blocks were further tested in 3rd party laboratory to check for strength and other quality parameters. Tests were carried out as per IS 2185, Part 1, for ascertaining average compressive strength, water absorption, dry density, dimensional accuracy, drying shrinkage and moisture movement. The test results summarised in Table 2 demonstrated that the quality of recycled concrete solid blocks produced using RCAs were at par in acceptance criterion used for normal solid concrete blocks made with naturally sourced aggregates.
Table 2:- Third-party rest reports on solid concrete blocks made with RCA (Fine aggregates) on physical properties of RCA
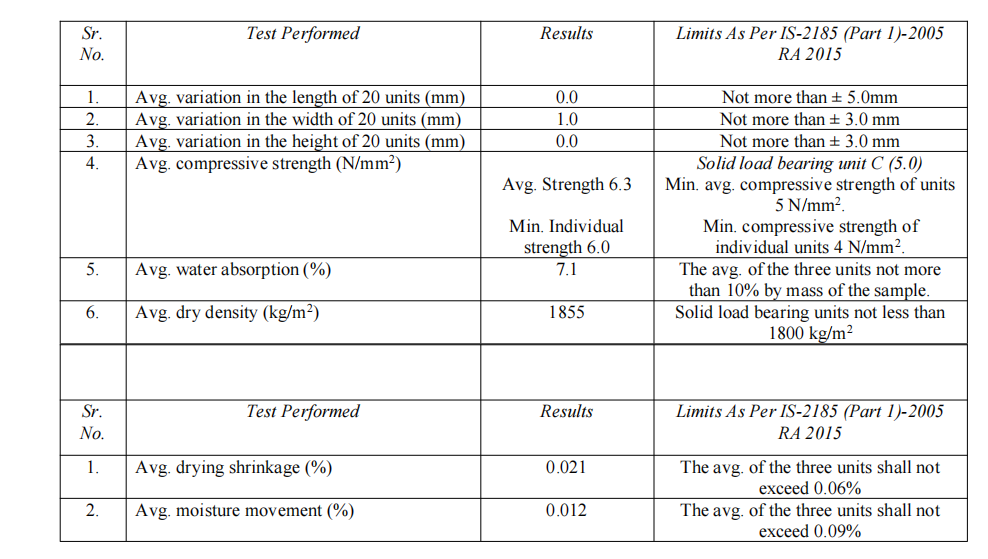
How to Promote Higher Uptake of Recycled Products?
The Construction and Demolition Waste Management Rules notified in 2016 by the Ministry of Environment, Forests and Climate Change (MoEF) have provided detailed guidelines to all concerned stakeholders including the state governments to address the growing concern of C&D waste. However, the actual implementation of these rules has witnessed multiple challenges. MoEF had proposed a 3-year action plan in 2019 for better governance, reduced landfill use, effective management of construction waste through recycling and to increase the focus on resource efficiency. Concerted efforts by Niti Aayog, MoEF, state governments and Urban Local bodies (ULBs) along with recent critical policy developments are expected to accelerate effective C&D waste management across various Indian cities.
To promote higher uptake of recycled products made using C&D waste in construction sector, it suggested that more emphasis is needed on the following aspects:
- the government should evolve and implement public procurement policy on recycled products
- the government should lower the GST slab rates for recycled products
- BIS/IRC should incorporate new guidelines in relevant building design codes and standards to encourage use of C&D waste right at the design stage of any project
- Incentivize all stakeholders involved in C&D waste management to provide financial benefits for better implementation of C&D waste rules and framework
- the government should also mandate the use of recycled products from C&D waste in all private and public infrastructure projects encouraging circular economy.
Incidentally, it is heartening to note that the Ministry of Road Transport & Highways (MoRTH) has recently taken few steps to finalize guidelines for value engineering during preparation of feasibility reports of proposed highway projects for promoting use of C&D waste.
Conclusion
Godrej Construction’s recycled concrete manufacturing plant is perhaps the largest such unit in India. As metropolitan cities like Mumbai grow older, C&D waste management is bound to become a major cause of concern for ensuring sustainable development within the city. Godrej Construction has taken an early lead to clearly demonstrate the Company’s commitment towards sustainable development and hope that many others in the industry will follow in the endeavour to build more sustainable construction products for the benefit of our future generations. The mindset of the industry needs to change towards adopting cleaner production practices, preservation of non-renewable raw materials and better construction methods following the principles of circular economy to help reduce energy intensity and carbon footprints of the construction sector.
References
- Roychowdhury, Anumita, Somvanshi, Avikal and Verma, Anurag ‘Another brick off the wall – Improving construction and demolition waste management in Indian cities’, Centre for Science and Environment, New Delhi, August 2020
- ‘Utilisation of recycled produce of construction & demolition waste: A ready reckoner’ C-FARM, New Delhi, and Building Materials & Technology Promotion Council (BMTPC), New Delhi, October2018.
Authors
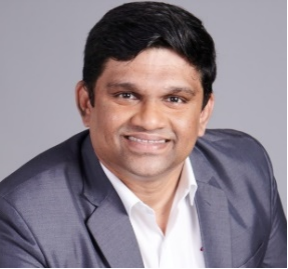
Mr. Abhijeet Gawde
Mr. Abhijeet Gawde a brilliant civil engineer from Shivaji University, is currently the Head-Business Development with Godrej Construction. He has multi-faceted professional experience of over 17 years in different spheres of infrastructure and special projects, with responsibilities ranging from design engineering, project execution, strategic planning and business development. He has worked on major infrastructure projects in India such as metro rail, expressways, marine and transportation sector and also possesses working experience on international projects in UK, UAE. Abhijeet has acquired the ability of driving the organic and inorganic business growth in the transport infrastructure and buildings sectors. He is known for forming successful JV’s, consortiums and associations by identification of suitable local as well as international partners. Exploring new technologies for sustainable construction and research into such technologies/materials continues to be his professional interests.
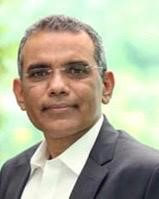
Mr. Anup Mathew
Mr. Anup Mathew heads Godrej Construction (GC), one of the 14 business units of Godrej & Boyce Manufacturing Co. Ltd (G&B). Mathew has over three decades of work experience in the construction and real estate sector. As the Head of GC, he is responsible for the construction and real estate business of G&B. He has helped conceptualize, plan, develop and maintain several million m2 of real estate assets, and allied built environment, in many locations across India. Anup is also responsible for managing the vast portfolio of corporate real estate assets of the organization. He is committed to the cause of promoting productivity improvement, sustainable development and safety related practices this Sector. In the year 2012, Anup was awarded a Fulbright Scholarship and completed his assignment from Carnegie Mellon University, USA. He also has a Diploma from the Swedish Institute, Stockholm, Sweden. Mr. Mathew is also the Chairman of the Board of Directors at the Institute for Lean Construction Excellence (ILCE), India. He is also Chairman of the IGBC Net Zero Waste Committee.