Water is an essential ingredient of concrete. It performs three important functions. Firstly, it helps in mixing different ingredients of concrete, lubricating the mix and providing the desired workability for placing and compaction. Secondly, water is also required for washing and cleaning of the mixer and other implements, and thirdly for curing of concrete so that concrete achieves desired properties in its hardened state.
No authentic data is currently available on the amount of water needed for these three activities. In absence of such data, an attempt is made in this write-up to initially arrive at a very rough estimate (a sort of guesstimate) of the total water requirements for concrete production in India and then highlight major steps to minimize/conserve the usage of water.
Introduction
The experience from the ready-mixed concrete (RMC) industry may be useful in having some broad idea of the water requirement for two categories, i.e. for mixing concrete and for washing and cleaning the central and transit mixers and other tools used in concrete production. When setting up a new RMC plant, it is a common practice to make provision of around 300 to 400 litres/m3 of water to satisfy the requirements of these two categories. Based on the assumption that approximately 10% of the cement produced in the country (i.e around 35 million tonnes/annum currently) is routed through the captive and commercial RMC plants in the country, the total volume of concrete produced in India currently stands somewhere in the range of 100 to 120 million m3/annum.
Water Requirement during Production of Concrete and other Cementitious Products
Let us consider an average figure of 350 litres/m3 of water requirement for a typical RMC plant in India. Taking into account this requirement, the 100-120 m3/annum concrete produced from RMC plants in India would roughly be consuming 35 to 42 billion litres of water per annum. This requirement pertains to the conversion of merely 10% of the total cement production into concrete and concrete products
For the remaining 90% of cement conversion to concrete and other cement-based products, the absence of any reliable data compels us to make a ‘guesstimate’ which in the opinion of the author, may at least be in multiple of 10-12 times that of the water consumption of concrete produced from RMC plants. A slightly higher multiplication factor of 10-12 is considered in the guesstimate as considerable water is wasted in the production of labour-oriented site mixed concrete and plastering work. Thus, the total water required for conversion of the entire cement production into concrete and cement based products would roughly be in the range of 420 to 500 billion litres/annum! This is certainly an enormous quantity of water which highlights the urgent need of water conservation. (This guesstimate does not include the amount of water used in the production of cement.)
Water Requirement for Curing
Water is also used for the curing of concrete – an essential requirement to achieve desired properties of concrete, mainly the compressive strength and durability. The age-old method of external curing, which is in vogue in India, involves adoption of either the water ponding over freshly laid concrete surfaces or covering them with wet burlaps. In actual practice, curing is unfortunately one of the most neglected areas in concrete construction. In spite of the clear guidance in IS 456, specifying a minimum of 7-day wet curing for concrete using OPC and 10 days for concrete using mineral admixtures, curing period is quite often shortened in actual practice, mostly for achieving faster construction or other needs.
Further, there is no guidance on the quantity of water to be used for curing. Private guidance from few senior colleagues in construction sphere revealed that curing with water ponding and that with hessian cloth would require approximately 5 litres/m2/day and 3 litres/m2/day, respectively. Of course, the local conditions of ambient temperature and humidity will govern the actual water requirement for curing. However, for the guesstimate, let us assume an average of 4 litres/m 2/day of water requirement for curing. Let us further assume that the average duration of curing would be 3 to 5 days at the national level. With these assumptions, the approximate quantity of water required for curing concrete surface having 1m2 area would be 12-20 litres/m 2
A recent report predicts that India would witness around 30 billion m2 of construction in urban area by 20401. This means approximately 1.5 billion m2 of construction/year.
Considering that the majority of this construction would happen with concrete and also considering the rough estimate of 12-20 litres/m2 of water would be required for curing, the yearly total water requirement for curing of concrete would be around 18-30 billion litres/annum up to 2040.
The very rough estimates of water requirements mentioned in the above paras may be considered as purely tentative. The objective of this exercise is to underline the fact that substantial amount of water is getting consumed in concrete construction and that there is an urgent need to look into the ways and means to minimise the same.
Incidentally, India’s national institutes and the research community in the country need to undertake pilot studies to arrive at the correct estimates of water requirements in the construction of buildings, roads and bridges, flyovers, etc.
Measures for Water Conservation
Water required for various construction activities needs to be fetched from the locally-available sources. The effective and economical use of the available water is the key to achieve sustainability. Some of possible ways to reduce the unwarranted use of water during the entire production process involving concrete are briefly enumerated below.
Optimising use of mixing water in concrete
Optimizing the paste content (i.e. total cementitious content and water content) in concrete is crucial for achieving the specified compressive strength, durability and other desirable properties in concrete. Quite often, the cementitious content in concretes produced by RMC plants is on the higher side than necessary. Many specifiers tend to provide the so-called ‘safety margin’ in specifying the cementitious content. This is borne out of the concern that the concrete may not be able to achieve the specified strength.
In site-mixed concrete, there is minimal or no control on the water used in production! There is a tendency amongst field-based technicians and supervisors to use very high-slump concrete (‘patala mal’ in colloquial language ) so that placing and compaction become easy. Further, there is also a tendency to use ‘extra’ cement to cater to the lower degree of quality controls at site.
Excess amount of cement or cementitious material content demands extra water, leading to excess paste content in the concrete mix. This gives rise to higher shrinkage in concrete which is responsible for the cracking and strength reduction. This, in turn, is detrimental from long-term durability perspective.
Therefore, the concrete mix design needs to be optimised to have only the bare necessary cementitious and water contents. In addition, careful attention is needed in the production of concrete to ensure that the specified water-binder is not exceeded during the production, placing and compaction of concrete.
Use of Water Recovered from Reclaimer and Filter Press
In earlier paras, it was mentioned that nearly 300-400 litres of water is used by RMC producers in the production of 1 m3of concrete. Assuming that mixing of concrete consumes nearly 50% of this water, the remaining water, which is stored in a drum mounted on the top of the transit mixer, is poured into the mixer after discharging concrete at site. This is usually done with a view to keep the blades and inside portion of the drum free from the build-up of cementitious materials. Once the transit mixer comes back to the RMC plant, the wash water from the mixer drum is poured in the settlement pits, Fig 1 (left). These pits usually have two or more compartments, permitting the transfer of relatively clear water from one pit to the other. This relatively clear water from the pit is re-used mostly for dust control and other cleaning activities in the plant. However, in view of the high turbidity of such water, the re-use of this water is happening in an inefficient manner currently.
A few environmentally-conscious RMC plants, mostly located in big cities, have started using a “Reclaimer” system, which is capable of separating coarser materials from returned wash water, thus discharging less turbid water in to the settlement pits, Fig 1 (right). The use of reclaimer system is certainly a technical advancement over the mere use of settlement pits. Yet, the reclaimer system is not able to remove the finer fractions from wash water completely and the extracted material from the reclaimer .contains considerable moisture, which hinders its direct reuse in concrete
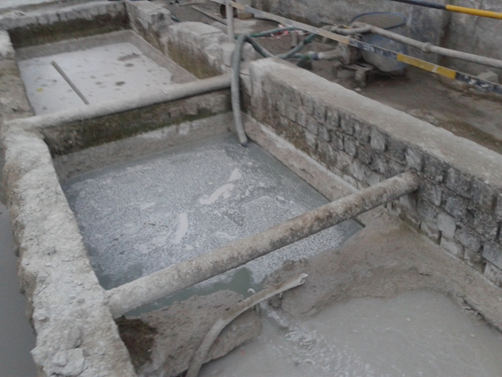
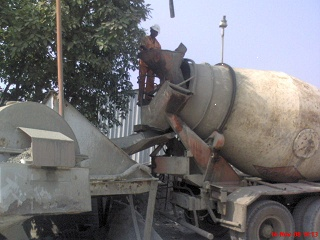
Fig 1 Conventional settlement pits (left); Wash water from transit mixer being poured in a Reclaimer (right)
Filter-press System
In addition to the adoption of the ‘Reclaimer’ system, the use of an innovative ‘Filter-press’ system has commenced in India on a pilot-scale. The filter-press receives wash water from the reclaimer and squeezes the same powerfully. As a result, the water coming out from the filter-press is cleaner, removing almost the entire finer fractions from the wash water. Further, the moisture content in the extracted sludge from the filter-press is quite low, which can permit its re-use back into concrete, thus achieving the final objective of ‘zero discharge’ from RMC plants!
The provision of the ‘Reclaimer’ and ‘Filter-press’ system will certainly require additional capital investment; however, it is claimed that the extra investment can be recovered in 3-5 years! The RMC producers in the India should start establishing the ‘Reclaimer’ and ‘Filter-press’ system in their plants, at least in big cities.
Use of Innovative Chemical Admixtures
The development of hydration-stabilising chemical admixture (HSCA) helped RMC producers to effectively extend the working time of fresh concrete, especially when concrete is to be used for long-haul or hot-weather applications.
It is now reported that recently a one-component engineered polymer admixture referred as RCT has been developed for converting the returned concrete into a very low-strength granular material2. Such granular material can be used as backfill, road base or in other applications. The incorporation of RCT permits the beneficial re-use of returned concrete. It is claimed that with the use of both HSCA and RCT, concrete producer are in a position to manage the returned concrete beneficially, reducing concrete waste and operational costs. It is also claimed that HSCA and RCT have the potential to reduce the carbon footprint of concrete and promote sustainable construction.
In India, large-scale commercial use of HSCA has not been reported. RCT is just recently introduced admixture in the advanced countries.
Internal Curing of Concrete
“Curing” is a process of preventing loss of moisture in freshly placed concrete to allow hydration of the cementitious materials to occur so that concrete is able to develop the desirable properties. As pointed out earlier, the lack of adequate curing will lead to a host of problems such as lower compressive and flexural strengths, lower surface hardness and abrasion resistance, higher permeability and absorption (hence lower durability), surface cracking, etc.
Considerable negligence happens in the external curing of concrete at construction sites. Acute-to-moderate shortage of water at some locations in the country may be one of the reasons for this.
The topic curing has attracted attention of the research community and considerable R&D work has already been done in this area3. There are two alternatives to external curing: internal curing and internal sealing.
Internal curing of concrete can be achieved by using either water-saturated aggregates or super absorbent polymers. Light-weight aggregates having high porosity such as sintered fly ash aggregates or bloated clay aggregates have been used for internal curing. Super-absorbent polymer is used as concrete admixture during mixing. In both these methods, water from saturated aggregates or from polymers is slowly released within as the hydration process progresses.
Internal sealing involves adding water-soluble chemical during mixing of concrete. Such addition reduces water evaporation as concrete is exposed to air drying.
The construction industry in India will benefit in a big way if internal curing and/or internal sealing compounds become available in cost-effective manner. Such material would not only conserve the water presently used for curing of concrete but would go a long way in improving the performance of concrete, especially its durability.
References
- International Energy Agency, India Energy Outlook-2021, World Energy Outlook Special Report, https://www.iea.org.
- Charles Nmai, Chris Eagon, John Luciano, Innovative Admixtures to Address Operational and Sustainability Issues with Returned Concrete, ACI SP-355: Recent Advances in Concrete Technology and Sustainability Issues, pp.325-336.
- RILEM TC 196 ICC, Internal Curing of Concrete: State-of-the-art Report, 2007.