A. Yes, I agree with you. RMC industry has grown rapidly during last two decades in India. As we all know, ‘Concrete Slurry Waste’ is unavoidable. It is prohibited from being dumped on dumping sites due its harmful impact on environment. There are sound reasons why the RMC industry should consider proper disposal of wash water and sludge as an integral and important part of RMC plant operations. The advantages are numerous. Besides minimising the harmful impact on environment, systematic disposal of wash water and sludge improves the health and safety of personnel working in the RMC units, brings cleanliness in working environment and what is more important, is the saving in materials leading to cost saving in operations.
Expert Interview
How to Improve Effective Water Utilization and Sludge Disposal from RMC Plants?
Q.1 You are aware that the ready-mixed concrete (RMC) industry has grown rapidly in India during the last two decades. It is reported that the total concrete produced by the industry has reached a level of around 100-120 million m 3/annum. Can you briefly highlight the broad practices adopted currently by the industry in the recycling, reuse and disposal of the wash water and sludge generated during the production of RMC ?
In my opinion, there are two main reasons why the RMC industry has not focused attention on recycling, reuse and disposal of wash water and sludge generated during production of RMC. First, there is a lack of adequate awareness about the long-term detrimental environmental impact of neglecting proper disposal of concrete slurry. Secondly, the latest technological advancements have not been grasped fully by the industry personnel. Further, the implementation of statutory regulations on wash water and sludge is neither uniformly stringent nor meticulous. Therefore, broadly speaking, the wash water and sludge disposal management has remained a neglected, low priority area in operations and maintenance and the last option during capital expenditure at project stage.
Fortunately, there are some forward-looking RMC players from the organised sector who have established reclaimers in their plants in metro cities for separation of coarse material from wash water before discharging the water to the settlement pits. . Even after the removal of the coarser materials, the water discharged to the settlement pits still remain turbid and is mostly used for sprinkling and washing. The use of a reclaimer does not solve the problem of sludge disposal, Hence ‘Reclaimer-cum-Settlement Pit’ is not able to provide a complete solution .
Even this ‘Reclaimer-cum-Settlement Pit’ solution is not implemented or completely neglected in low-capacity, low-capex plants, mostly by captive RMC plants in non-metro cities.
Q.2 We understand that a few RMC plants in metro cities have installed ‘Reclaimer’ system for separating the coarser materials from the wash water before it is poured in the settlement pits? What are the main advantages of using Reclaimers?
A. I have already answered this question partly. Yes, the reclaimer helps in recovering the coarse and fine aggregate and the coarser faction of supplementary cementious materials like fly ash, etc. The extracted material can be recycled once it is partly dried. The reclaimer also reduces the load on settlement pits. Well designed and well-maintained reclaimer system helps in recovering most of the coarse and fine aggregate quickly from the returned / rejected concrete.
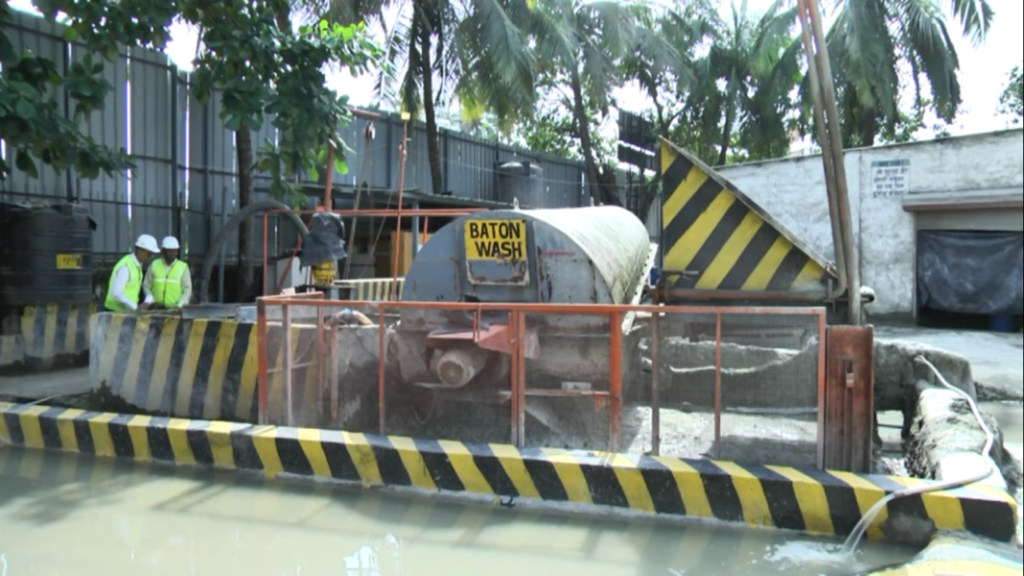
A Reclaimer set up in a RMC plant
Q3. Do you have a rough idea about how many RMC plants have been using the Reclaimer system?
A. Frankly speaking, we do not have an accurate, authentic data with us. We are aware that some RMC players from the organised sector have installed reclaimers in their plants in metro cities.
Q.4 Which are the main difficulties in reusing the material extracted from the “ Reclaimers- Settlement Pit “ in the production of RMC?
A. Presently, good reclaimers with efficient, modular design are available in India. However, in spite of the efficiently operating reclaimers, challenges of handling and reusing slurry water and sludge remain and this is one of the main pain point of RMC industry at the moment.
Sludge handling is a messy, painful and dirty and unsafe operation for the labour force. Since sludge contains considerable amount of water, it is difficult to handle and transport. Hence ‘De-watering’ of sludge is essential to recycle or to dispose of sludge responsibly. We need to reduce the water content in the sludge. A ‘Filter Press’ is a mechanical equipment used for ‘De- Watering’ sludge.
Q.5 What is a ‘Filter Press”? How does it work?
A. Filter press is ‘a Solid-Liquid’ separator that uses the pressure developed by slurry pump against the filter cloth. Solids from the sludge build up on the filter cloth, forming a cake. The filtrate (Water) exits the filter plates, yielding clean filtered water. Once the chambers are full, the cycle is completed and filter cakes are ready to be released.
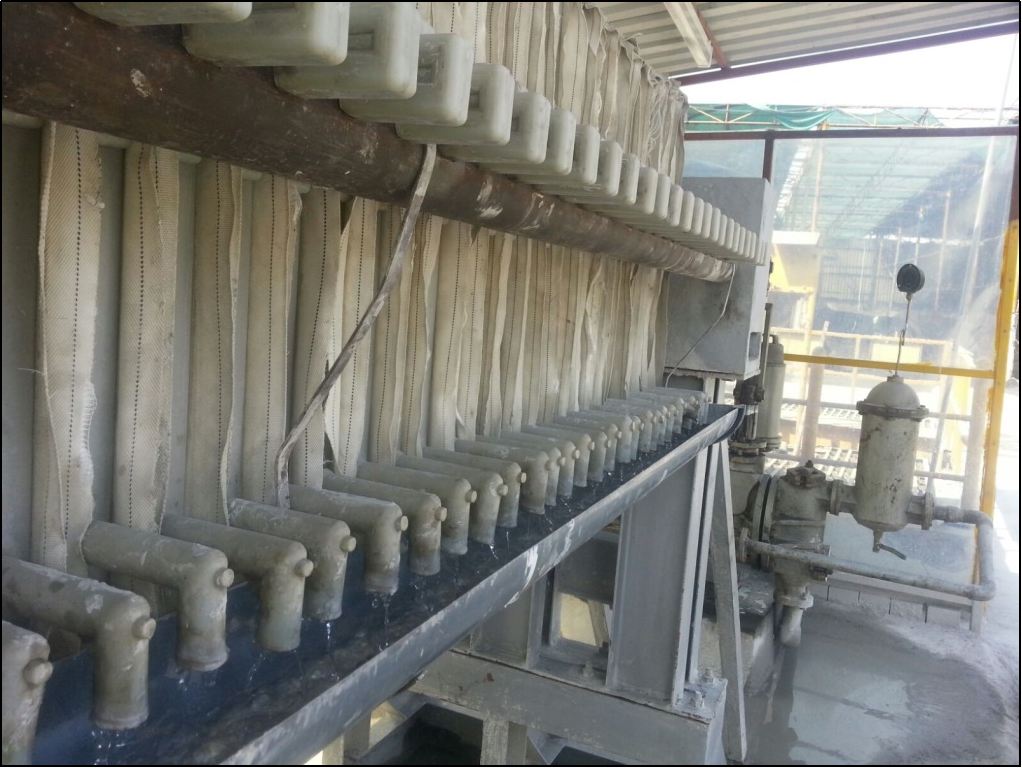
A typical filter press unit which delivers clean water and sludge cakes from washwater
It is a batch-type operation. With automation introduced in to the system, the filter press runs continuously without any difficulty. It’s simple in construction, and the operations are easy and safe.The final output in the form of a cake is ‘Dry and Compacted’.
The use of both reclaimer and filter press will eliminate the need of settlement pit / pond etc. and associated messy, painful and dirty operations in RMC plants.
Q.6 Can the sledge cake coming out from the Filter press be used directly in the production of RMC?
Yes, the dewatered cake is easier to handle. This cake contains powdery material and some fine aggregate. The cake can be used in the production of RMC as a sand replacement in small proportion under the technical advice of the experts involved in concrete mix design. Already a few reputed, progressive RMC players in India have used filter-press on a trial basis.
Q.7 How clean is the water extracted from the operation of the Filter press? For which operations can such water be re-used in the production and use of RMC?
The water from filter press is reasonably clean. Visual inspection shows that the turbidity of the water is drastically reduced. Hence this water can be an integral part of the operations of RMC plant to save infusion of fresh water. Here, I would like to request the academic and R&D community in India to come forward and conduct comprehensive study on the quality of the water obtained from filter press. Such study will go a long way in clarifying doubts on the quality of water from filter press.
Q.8 How much period is needed to recover the initial investment and maintenance costs of the Reclaimer and Filter press systems?
Many case studies are available from developed countries like Singapore, Japan & Europe.
In the Indian context, we are working with a few reputed, progressive RMC players to prepare real life case studies with respect to investment, operational cost and rate of returns over investment etc. Hopefully, we will be in a position to share more information on this aspect in the near future.
Q.9 In your opinion, what sort of regulatory mechanism is needed to ensure the widespread use of the Reclaimer and Filter press systems by RMC producers so that the same results in ‘zero discharge’ from RMC plants?
As concrete slurry is unavoidable and integral part of RMC operations, it should be handled responsibly.
The central and state pollution control authorities have already specified to implement ‘ ZERO – Pollutant Discharge’ from RMC plants with respect to air , water and solids. Awareness should be created by the regulators for uniform implementation of the present statutory regulations. This will reduce harmful impact on environment and will save precious water.